In the rocky highlands of northern-central Saudi Arabia, granite resources are abundant but widely scattered across difficult terrain. Traditional stationary crushing lines are limited by long construction cycles and poor mobility. To overcome these constraints, a 150–200t/h granite portable crushing and screening system was deployed to handle high-hardness, abrasive stone materials while supporting rapid deployment and multi-site operations.
Granite Crushing Challenges
Granite is a hard rock with compressive strength ranging from 120 to 250 MPa, rich in quartz and feldspar. This makes it highly abrasive and difficult to crush efficiently. Common issues include excessive wear on equipment, poor particle shape, and low throughput if crushing systems aren’t properly configured. Effective processing requires high-strength structural design, precisely matched chamber geometries, and advanced wear-resistant components.
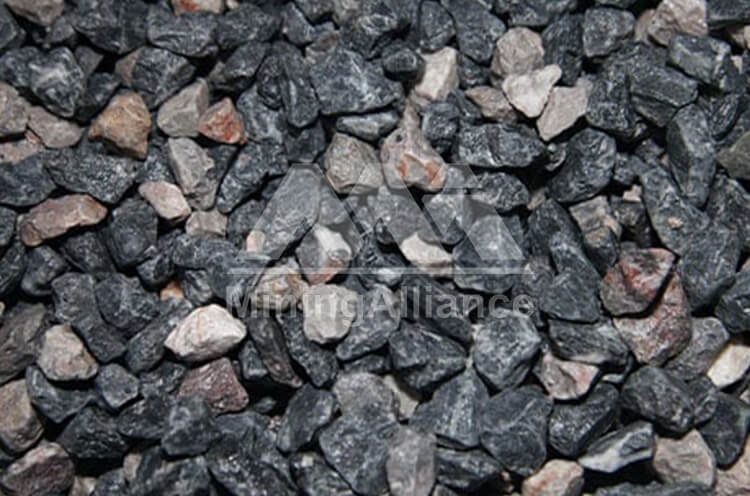
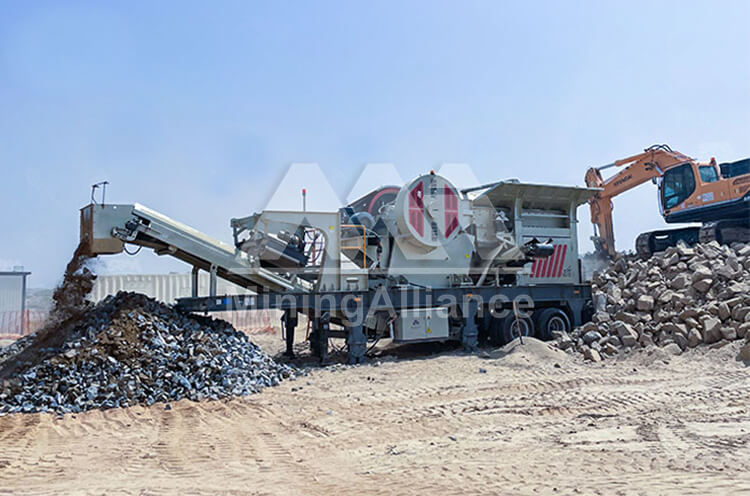
System Configuration
The portable plant uses a dual-stage crushing and closed-loop screening system, Its modular design allows flexible configuration according to terrain or integration with existing systems. comprising:
- Trailer-mounted heavy-duty jaw crusher (primary crushing)
- Mobile transfer belt conveyor
- Multi-cylinder hydraulic cone crusher (secondary crushing)
- Triple-deck high-frequency vibrating screen
- Return conveyor & finished material transport system
- Automated control and hydraulic regulation module
Technical Highlights
1.Adaptive Structural Engineering
Built on a reinforced steel chassis, the unit performs reliably in hot, dusty desert conditions. All components are integrated into a single control platform for synchronized start/stop and simplified on-site mobility.
2.Optimized Dual-Stage Crushing
The primary jaw crusher handles coarse material, while the secondary cone crusher features a deep crushing cavity and pressure-compensation hydraulics to maintain consistent throughput and ensure better aggregate shape.
3.Wear-Resistance Enhancements
Jaw plates, mantle, and bowl liner are made with manganese alloy composites, extending wear life by 40% compared to conventional materials, reducing maintenance downtime significantly.
4.Particle Quality Assurance
The high-frequency vibrating screen features intelligent amplitude and frequency adjustments, producing cubical aggregates with well-controlled gradation—ideal for concrete, asphalt, and road sub-base applications.
5.Environmental and Monitoring Systems
Equipped with atomized dust suppression, noise dampeners, and remote diagnostic support, the unit complies with Saudi Arabia’s updated mining regulations, ensuring environmental responsibility and efficient fleet management.
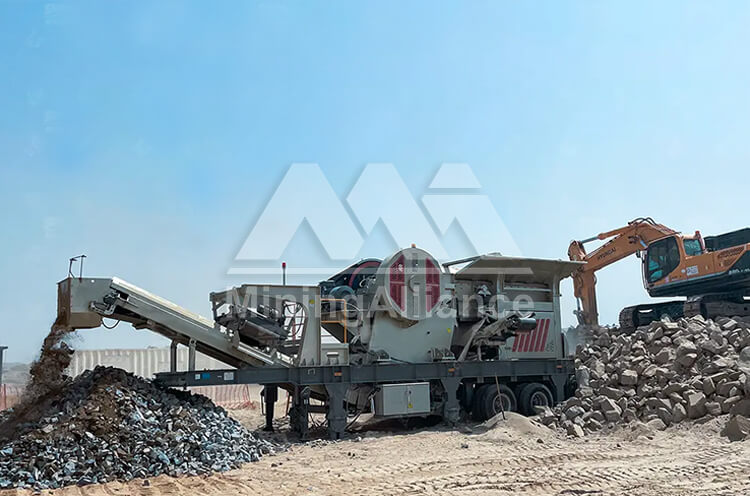
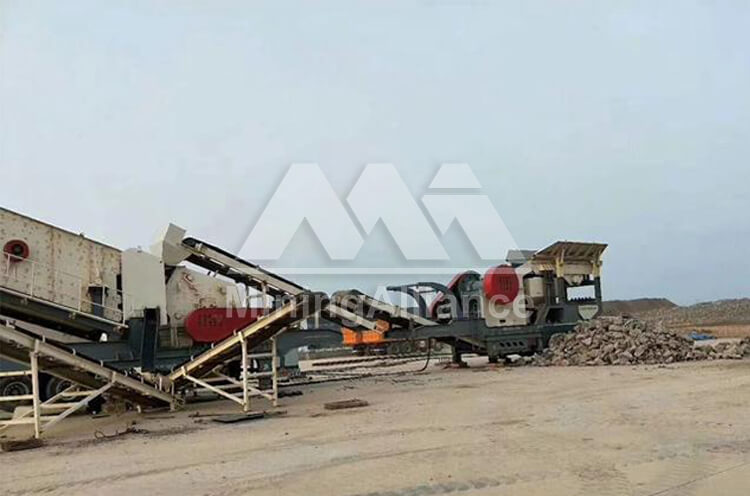
Project Outcome & Feedback
This plant is currently operating in the Asir region for a granite mining contractor. Daily uptime exceeds 14 hours, with finished material sizes between 0–31.5 mm. Operators report low fuel consumption, minimal recirculation, and consistently high-quality output. The client is now planning to expand with a second plant for another site based on the system's success.