With infrastructure development accelerating across Africa, granite has become a key raw material for high-strength, wear-resistant construction aggregates. This project in Mali, West Africa, was designed to supply high-quality crushed stone for a local road enhancement initiative. Given the short project cycle and frequent site relocation, the client opted for a 50–80t/h portable granite crushing and screening plant, which enabled fast commissioning and cost-effective mobility.
Environmental Challenges in Mali
Located in landlocked West Africa, Mali features hot, dry climates, large temperature fluctuations, and underdeveloped roads and power infrastructure. Stationary crushing systems often struggle with transport complexity, lengthy deployment, and maintenance needs. In contrast, this portable setup leverages flexibility, integration, and intelligent control, making it highly suitable for small to medium-scale mining and construction tasks in Mali.
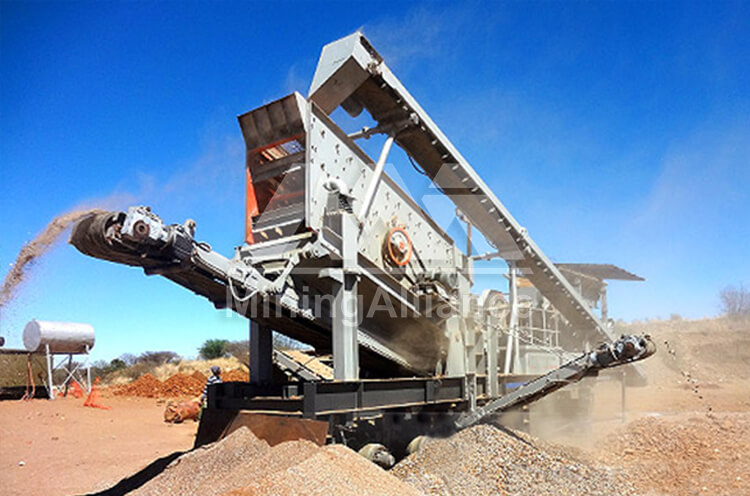
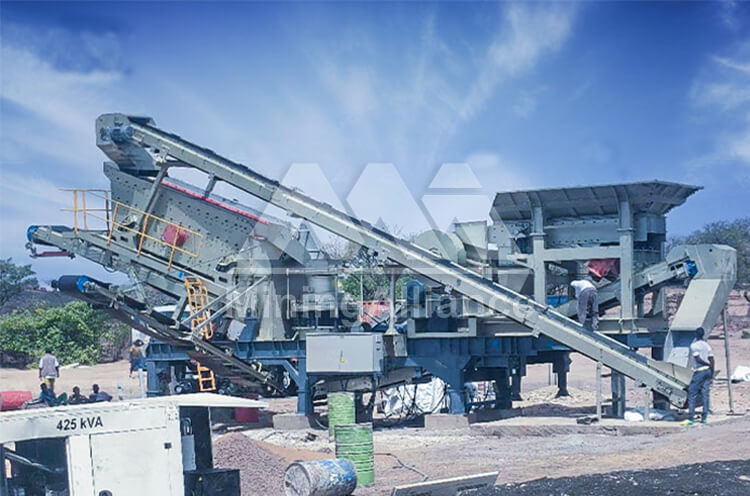
System Configuration
The plant is designed to handle granite blocks ≤400mm in size and process them into well-graded aggregates. This compact layout streamlines the process flow, improves production efficiency, and allows rapid setup in tight or rugged spaces. Configuration includes:
- Wheeled chassis for mobile deployment
- Heavy-duty jaw crusher for primary crushing
- Single-cylinder hydraulic cone crusher for secondary crushing
- Two-deck circular vibrating screen with recirculating conveyor
- Diesel-electric integrated control system
Technical Features and Adaptability
1.Lightweight Modular Design for Easy Mobility
The system uses modular, bolt-together construction, eliminating the need for heavy lifting equipment. On-site setup and commissioning can be completed within 24 hours, significantly reducing preparation time.
2.Diesel-Electric Hybrid for Remote Operations
The dual power mode allows operation on both generator and grid power, ensuring continuous production in areas with unstable electricity supply, ideal for inland African regions.
3.Optimized for Abrasive Material Crushing
Granite’s hardness and quartz content demand highly durable machines. This system features manganese-steel and alloy-based components in both jaw and cone crushers, offering long service life under tough conditions.
4.Precision Screening & Closed-Loop Design
A double-deck vibrating screen ensures clear classification of aggregate sizes and reduces flake content, meeting road-building standards. The closed-loop conveyor helps maintain consistent particle quality.
5.Smart Control & Remote Diagnostics
The PLC-based control system automates startup, protection, and monitoring. Real-time alerts and performance adjustments reduce human error and support efficient site management.
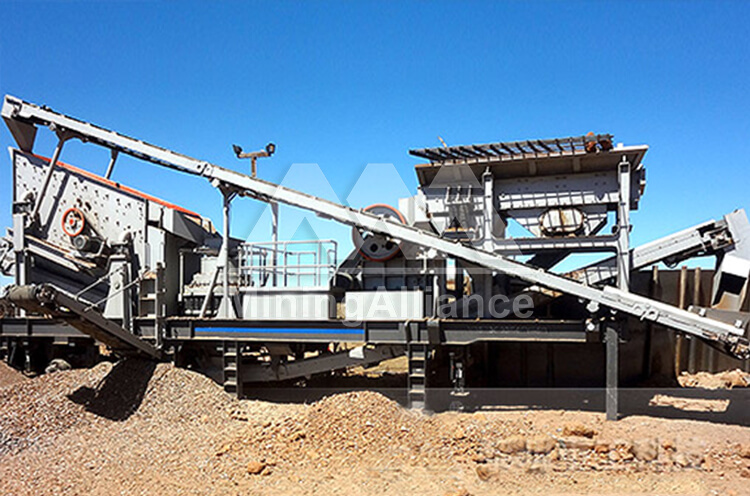
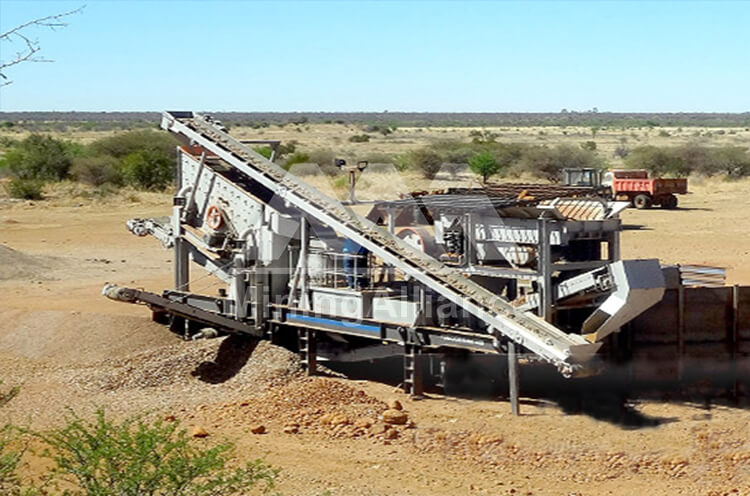
Performance & Client Feedback
Post-commissioning, the plant has maintained a steady output of 55–75 tons per hour over 10+ hours of daily operation. Clients report excellent aggregate shape and suitable gradation for sub-base and concrete batching. With stable fuel consumption and reliable performance, the client is now planning a second unit for another quarry site.