Andesite, known for its high hardness, compressive strength, and cohesive properties, is an ideal material for producing high-grade concrete aggregates. It is commonly used in the construction of highways, airport runways, and water conservancy facilities. A major construction material supplier in Indonesia required a high-capacity, rapid-deployment crushing solution for infrastructure projects in Sumatra. The client selected a 400t/h wheeled portable crushing and screening plant specifically tailored for andesite processing.
Crushing Challenges and Selection Criteria
Due to its intermediate to high hardness (compressive strength of 100–150 MPa), andesite poses several processing challenges such as:
- High stress on crushing components
- Fast wear of parts
- Risk of clogging due to moisture and stickiness
- Requirement for high throughput and flexible deployment
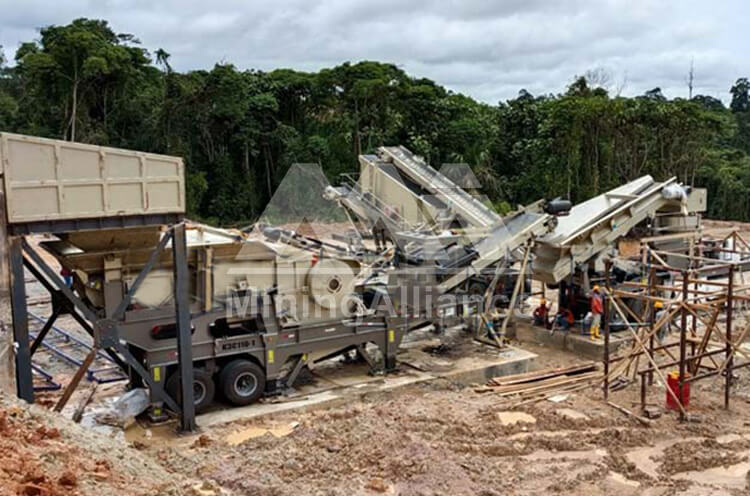
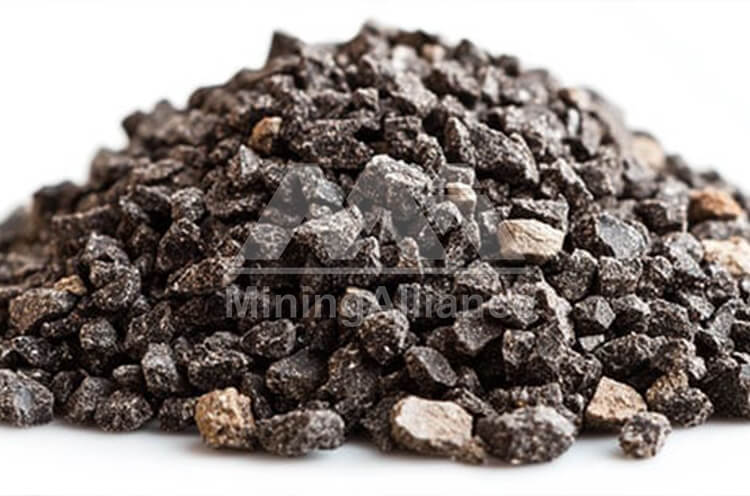
Configuration Overview
This modular plant comprises four wheeled units for rapid transportation and on-site setup. This configuration supports stable production of up to 400 tons per hour and enables accurate classification of aggregate sizes for multiple construction applications.
Technical Highlights and System Advantages
1.Modular Design for Mobility
Trailer-mounted units allow quick relocation between sites, enabling seamless transitions for multiple projects.
2.Multistage Crushing for Andesite
The triple-stage crushing setup (jaw + medium cone + fine cone) ensures continuous high-efficiency processing with optimal particle shape.
3.Anti-Wear Construction for Longevity
Wear components are made from manganese alloy steel with reinforced seals and cooling systems, ensuring reliability in tropical heat.
4.Smart Centralized Control
A PLC-integrated control unit enables real-time monitoring and automation, optimizing feeding rate, temperature, and electrical load with minimal human input.
5.Moisture-Resistant Screening System
The powerful triple-deck screen with anti-stick mesh and auxiliary cleaning units prevents clogging from moist, sticky materials.
6.Comprehensive Environmental Controls
Misting systems, noise barriers, and vibration-damping components minimize environmental impact and enhance operator safety.
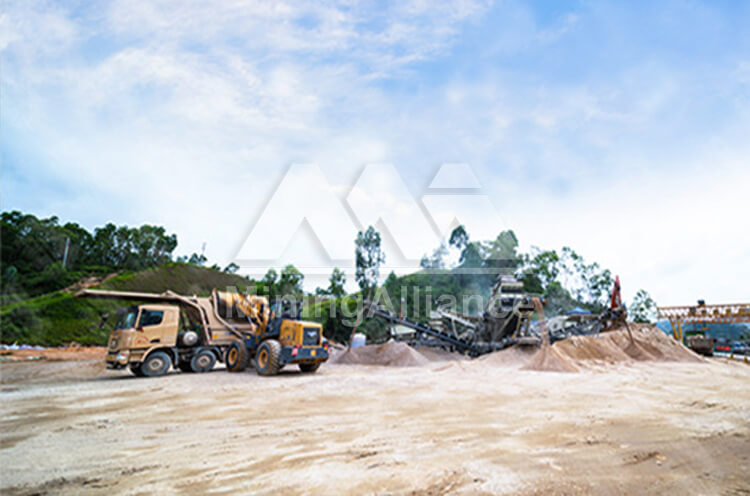
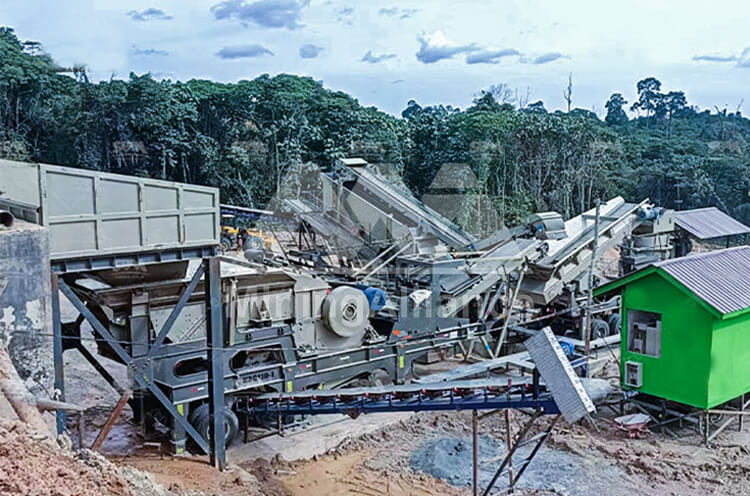
Operational Performance and Feedback
Post-commissioning, the system consistently produced 7,500–8,000 tons of aggregates daily. The client reported high machine uptime, long-lasting wear parts, and low labor costs—typically requiring just one control operator and two inspectors per shift. The final products had excellent gradation and were immediately used in road bases, ready-mix concrete plants, and coastal reinforcement works. Plans are underway to deploy a second plant of the same configuration in Java.