As industries such as high-purity silicon, glass manufacturing, and photovoltaics rapidly expand, efficient processing of silica rock has become critical. This project introduces a 300t/h Silica Rock Portable Crushing Plant, designed with high-output, precision control, and superior mobility in mind. It’s engineered for use in remote quarries, high-altitude terrains, and flexible field deployments.
Equipment Structure & Crushing Flow:
The system includes:
- Tracked or wheeled mobile chassis
- Heavy-duty vibrating feeder
- Large jaw crusher (primary crushing)
- Multi-cylinder hydraulic cone crusher or vertical shaft impact crusher (secondary/tertiary)
- Triple-deck vibrating screen
- Centralized intelligent control panel
- Belt conveyors & onboard dust suppression units
Process Overview:
1.Raw silica rock is fed via loader into the hopper and evenly distributed to the jaw crusher for initial reduction;
2.The crushed material is conveyed to a secondary crusher to refine size and shape;
3.Vibrating screens classify product into various size fractions; oversize is recirculated for further reduction;
4.The plant is monitored and controlled through a smart PLC system for real-time diagnostics and feedback-loop optimization.
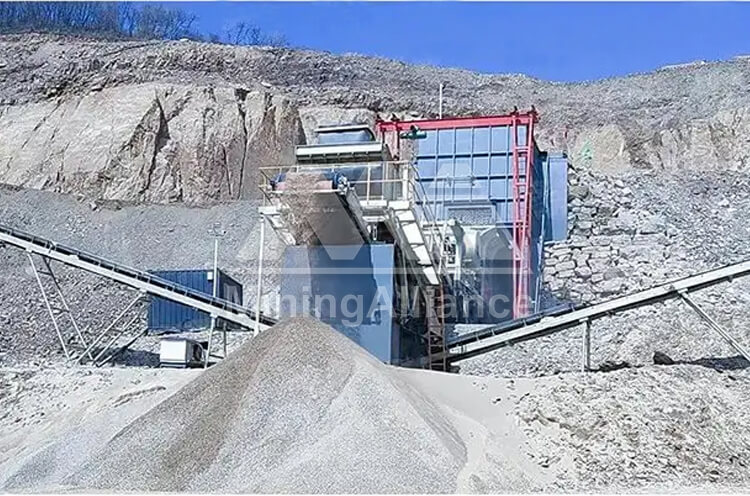
Technical & Operational Advantages:
- Wear-Resistant Engineering: Components facing direct impact use high-chrome alloy or ceramic-coated wear parts, ideal for highly abrasive silica;
- Shape Optimization: Combines laminated crushing and shaping stages to produce cubical aggregates with minimal flakiness;
- Energy Efficiency: Automated power regulation via load-responsive control reduces energy use by 15% compared to conventional systems;
- Rapid Relocation: Unified trailer-compatible modules enable fast setup and redeployment, perfect for short-term high-output projects;
- Environmental Compliance: Optional spray systems, dust collectors, and sealed hoods ensure compliance with strict emission standards.
Project Advantages
1.Reduced Investment:
The MK Semi-mobile Crusher and Screen (Skid-mounted) requires only leveling and compaction or a simple foundation, significantly lowering initial infrastructure costs.
2.Compact Footprint:
By cleverly utilizing the on-site terrain, the equipment occupies only 360 square meters.
3.Rapid Production:
All components, from raw material warehouses to finished product transfer equipment and electrical control facilities, feature a modular design, allowing for production to commence within one week at a new site.
4.Customized Design Service:
Given the material's exceptionally high abrasion resistance, all parts in contact with the material undergo customized wear-resistant treatment.
Project Performance:
Currently deployed at a silica mine in Southeast Asia, the system yields a daily output of 7,000 tons of well-graded, low-impurity silica aggregates, suitable for high-end processing. Its mobility, reliability, and user-friendly maintenance design have significantly lowered logistics and construction costs, making it a benchmark solution for portable silica crushing operations.
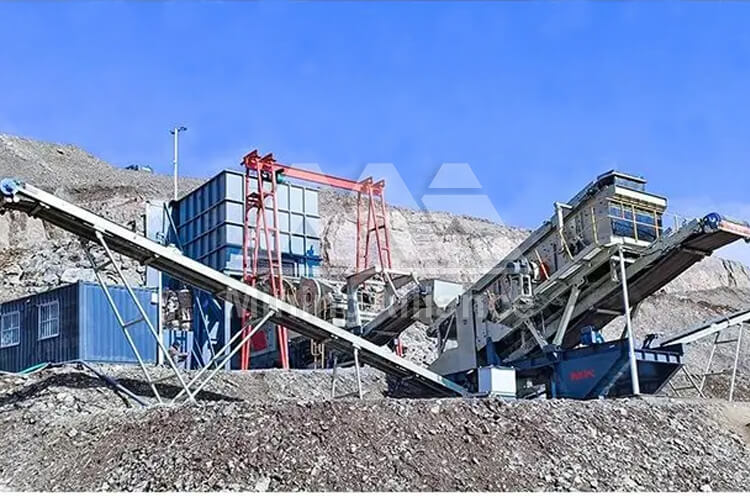
The customer's project involves silica rock with a silicon content exceeding 99.9%, characterized by high hardness, excellent abrasion resistance, and challenging processing requirements. Additionally, site constraints limit the operating space for equipment, and the project schedule is tight, spanning the Spring Festival, which further compresses the construction timeline.
After thoroughly understanding the customer's needs, MAM customized the MK Semi-mobile Crusher and Screen (Skid-mounted) for the project. MAM designed the overall operational area and process, providing comprehensive guidance for installation and commissioning, which ultimately ensured smooth production.